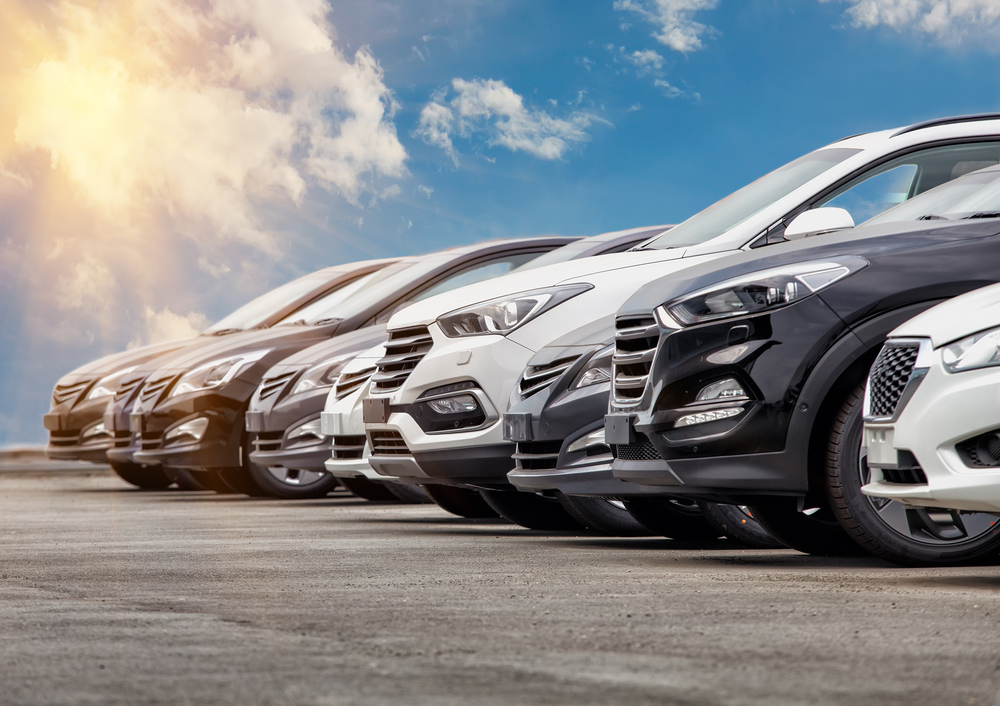
コンサルティング世界大手米マッキンゼーは9月18日、自動車のライフサイクルにおける二酸化排出量削減ポテンシャルを分析したレポートを公表した。自動車業界が協働すれば、追加コストなしで2030年までに材料生産から発生する二酸化炭素の66%を削減することができるとした。
マッキンゼーによると、現在における自動車産業の二酸化炭素排出量は65%から80%が走行時に排出されるもので、ライフサイクル全体の材料生産による排出量は18%から22%程度にとどまる。しかし今後、排ガスに含有される二酸化炭素の削減努力とEV普及に伴うバッテリー生産量増加によって、ライフサイクル全体に占める材料生産からの発生二酸化炭素が60%まで上昇すると予測。自動車業界はすでに排ガスの脱炭素化に着手しているが、今後ゼロ自動車を目指すには、材料生産段階での脱炭素化にも取り組む必要が出てくる。
材料段階での二酸化炭素排出量は、ガソリン・ディーゼル車の低炭素化ではアルミニウム及びプラスチック生産工程が重要で、追加コストなしで全体の60%の削減が可能とした。アルミニウム生産では、リサイクル素材利用拡大、新たな製錬技術の採用、使用電力の脱炭素化により、生産コストを下げながら二酸化炭素排出量の73%が削減可能。また、ポリプロピレンやポリエチレンなどの内部構造に使われるプラスチック素材のリサイクルで34%減、ナイロン・リサイクル技術の規模拡大によって、追加コストなしで全体の最大92%の削減が可能だという。
また残りの40%の脱炭素化はコスト増となるが、脱炭素型の電源を用いたアーク式電気炉による鉄鋼製練技法が広く実用化されれば、追加コストなしで達成することができるとした。製鉄の水素還元方式については、コスト削減、サプライチェーン構築、規制改革等を要すると指摘した。
また、工場立地についても、製造での二酸化炭素排出量が多い電気自動車(EV)バッテリーセル等を再生可能エネルギー比率の高い地域で生産すれば、さらにコスト削減しながら二酸化炭素排出量を37%削減できると分析。そのコスト削減で捻出できた資金でコスト増となる技術採用すれば、ガソリン・ディーゼル車と比べ、車両生産での二酸化炭素排出量をコスト増なしで66%削減できるとまとめた。
一方、これらの対策を講じるには、大きな障壁があることにも言及。一つは、自動車業界にまつわる広大な範囲のバリューチェーン全体が脱炭素に向けて協働する必要があること。特に前述の対策は、自動車業界ではなく素材メーカーでの対策の領域が多い。また、新技術が未だ量産化に向けた実用段階に至っておらず、多額の先行投資決断が必要となること、マテリアルフローが複雑で影響を追跡することが困難であること、などが課題として挙げられる。
さらに、各プレーヤーがばらばらに技術ロードマップを描いたのでは、非常にコスト効率が悪くなる可能性があり、自動車業界がリードしてバリューチェーン全体を協調させる必要があるとした。
【参照ページ】The zero-carbon car: Abating material emissions is next on the agenda
Sustainable Japanの特長
Sustainable Japanは、サステナビリティ・ESGに関する
様々な情報収集を効率化できる専門メディアです。
- 時価総額上位100社の96%が登録済
- 業界第一人者が編集長
- 7記事/日程度追加、合計11,000以上の記事を読める
- 重要ニュースをウェビナーで分かりやすく解説※1
さらに詳しく
ログインする
※1:重要ニュース解説ウェビナー「SJダイジェスト」。詳細はこちら